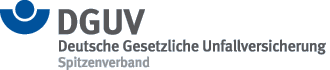
completed 01/1994
Stationary grinding machines are often used for material working. During the grinding process the abrasive wheels are subject to tension-, cutting- and centrifugal forces. The latter play a predominant role in terms of safety as they may cause bursting of the grinding wheel. Fragments of grinding wheels flung out of the working zone are likely to lead to serious accidents with persons injured and machines and equipment considerably damaged. Consequently, there are defined operating speed limits for grinding wheels, and the latter must also make proof of a minimum breaking strength. The investigation was aimed to determine to which point the breaking strength of grinding wheels depends on their design and composition.
Centrifugal tests were conducted to determine the breaking strength of vitrified and reinforced grinding wheels and to investigate the connection between the bursting speed and the modulus of elasticity or the flectional strength of abrasive wheels.
The bursting speed of a grinding wheel depends to a large extent on its design and composition. Higher bursting speeds are observed in connection with larger grain and bond volumes and smaller abrasive particle sizes. While no clear relationship could be identified between the modulus of elasticity and the bursting speed, the tests revealed an excellent correlation between the flectional strength and the bursting speed. It is easy to determine the flectional strength of material samples. This information then serves to calculate the bursting speed of flat grinding wheels. In the context of accident analyses it is thus possible to determine the bursting speed retrospectively even with just a few grinding wheel fragments.
Further informations:
metal working
Type of hazard:mechanical hazards
Catchwords:Mechanische Gefährdung, Prüfverfahren, Maschinensicherheit
Description, key words:vitrified grinding wheels, reinforced grinding wheels, grinding wheel design, breaking strength, mechanical strength, modulus of elasticity, flectional strength