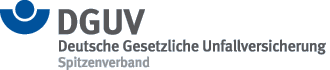
completed 10/2024
Milling machines are used in dental laboratories to machine parallel-walled surfaces on dental prostheses made of non-precious metal alloys. Cobalt, which is carcinogenic, is a major component in the non-precious metal alloys used for this purpose.
The German Social Accident Insurance Institution for the Energy, Textile, Electrical, and Media Products Sectors (BG ETEM) conducted a series of hazardous substance measurements on parallel-surface milling machines. The majority of these machines were not equipped with dust exhaust systems. The values measured show that in the majority of cases studied, the acceptable concentration of cobalt can be complied with; however, in some cases higher concentrations cannot be ruled out. Therefore, the use of equipment for dust collection and exhaust is recommended. This requires the current test specification for exhaust equipment used in dental laboratories (IFA-GS-M20) to be extended and a test method to be developed for determining the dust collection rate on parallel-surface milling machines featuring such dust exhaust equipment.
For a test method to be developed for parallel-surface milling machines equipped with dust exhaust facilities, tests must be planned, conducted, and the results evaluated. The existing test bench for dust collection equipment must be converted (adapted and extended) for tests on milling machines of this type. Material analyses must be performed by the IFA’s analysis department (IFA: Institute for Occupational Safety and Health of the German Social Accident Insurance). The developed test method must be described in the test specification (IFA-GS-M20).
In consultation with the BG ETEM and a manufacturer of dust exhaust equipment for parallel-surface milling machines, the existing test bench for determining the dust collection rate on dust exhaust intakes was converted, extended, and a test arrangement planned that resembled the conditions at real workplaces as closely as possible, while also having a high degree of reproducibility. Due to its higher hardness, much lower masses of the non-precious metal are machined than of the gypsum workpiece used in the existing measurement method. As a result, the new method was not able to measure the dust that was not collected (≈1% of the machined mass). The sampling/measuring point was relocated from the measuring channel of the test chamber so that the entire volume flow of the collected dust was drawn through a measuring filter (≈99%). In addition, the filter holder was optimised (polished inner surfaces, assurance of tightness by higher contact pressure), and tests with different types of measuring filters (membrane and glass fibre) were performed. The measuring filters used for the first test were membrane filters. These filters were observed to allow some of the dust to pass through before a filter cake is formed. Therefore, glass fibre filters were used as measuring filters in the subsequent tests.
The advantage of the new measurement method is that despite the brief durations of dust sedimentation, the measurement results exhibit much lower scatter than the measurement method previously used. The disadvantage, however, is that a special adapter is required to connect the filter holder to the manufacturer’s proprietary dust collection equipment. Whereas in the existing measurement method, dust sedimentation in the test chamber increases the probability of the test specimen passing the test, this effect is reversed in the new measurement method. At the BG ETEM’s request, comparative tests are to be performed in the future to clarify whether the existing test of exhaust intakes can also be converted to the new method. For this reason and due to other requirements related to revision of the IFA-GS-M20 test specification, a follow-up project is to be launched.
The bench tests conducted on the parallel-surface milling machines showed that at an exhaust volume flow rate of 54 m3/h, the dust collection rate exceeded 99% for one of the two collection elements studied and 97% for the other model (in each case with a probability of 95% in consideration of the lower confidence interval). The values obtained by the metal analyses for the dust collection rate in these tests exhibited greater scatter than the results of the gravimetric analysis. Glass fibre filters, in particular, which are advantageous for dust separation, possess high blank values and are therefore less suitable for metal analyses than membrane filters.
The test method developed was described in a new annex to the IFA-GS-M20 test specification. Once the final test specification has been produced (in the follow-up project), DGUV Test will be able to offer tests of the collection rate on dust collection equipment used on parallel-surface milling machines.
precision mechanics
Type of hazard:dangerous substances
Catchwords:carcinogenic substances, prevention, exposure