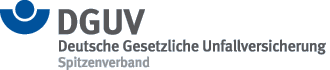
completed 08/2005
Several hundred accidents occur each year in Germany involving the use of circular saws and resulting in injury, in some cases permanent, to hands, fingers or thumbs. Attempts have been made in the very recent past to find solutions involving rapid stopping/lowering of the saw blades, and detection of hazardous situations by exploitation of differences between the respective capacitive impedances of limbs and workpieces. As yet, however, such solutions do not provide adequate protection, in particular where larger saws are involved. In the present project, new ideas for the prevention of movements leading to hazards and for non-contact detection of fingers were intended to permit comprehensive and economical protection on circular saws. The basic principles may also be applied to other manually guided machines.
Within a pilot project conducted jointly by the information technology division of FH Bonn-Rhein-Sieg and the BG Institute for Occupational Safety and Health (BGIA), principles for solutions involving video images were studied systematically with regard to their effectiveness for use in safety applications. The first planned stage of development involved the detection of upper limb extremities within a defined hazard area by means of a computer-aided video image analysis. A coarse-to-fine strategy was implemented in the image analysis, and its reliability tested. Based upon the position of the saw operator, the shoulder/arm area was first to be detected, followed by the hand and wrist area, which in turn was to permit detection of the individual fingers/thumbs. The purpose of this strategy was to ensure that reliable data are provided at all times on the location of endangered limbs. The principle was combined with other sensors in order to increase the reliability of detection. In particular, sensors were employed for measurement of the thermal radiation from the hands. In addition to finding a reliable and safe solution to the problem at hand, a further objective of the pilot project was to permit conclusions regarding the reliability and safety of a system solution based upon video image data. The application described here, which serves as an example, was to test the inherent suitability of video image-based analysis procedures for use in safety applications.
Studies have shown that an improved solution for safeguarding on circular and panel saws is already possible. The following sensor types were studied systematically for identification of sensors suitable for distinction between fingers/hands and wood: passive infrared sensors, field sensors, laser triangulation sensors, spectral photometers and laser scanners. Video sequence analysis was also studied. The combination of a field sensor (capacitive alternating field, coupled to the user through a floor mat) and a passive infrared sensor is the most suitable solution for reliable detection of the hands. The studies of the spectral photometer are very promising, but could not be completed in the context of project. When retrofitted to a circular saw in combination with a newly developed safety shroud, the proposed diverse sensor principle results in safe working practice on the saw, thus reducing the accident rate on such machines. Although the costs for the prototype were in the order of €500, the material costs can be reduced to less than €250 in volume production. A retrofit kit for table and panel circular saws employed in joinery businesses could therefore be made available at a realistic price. In addition, the new safety concept is particularly useful during training. The safety measures prevent trainees in training workshops from acquiring bad working habits. Safe practices for operation of these dangerous machines are thus incorporated into training from the outset. Work on the use of video sequence analysis for operator detection, in particular, suggests applications well beyond those on circular and panel circular saws. In large assembly shops in which robots move freely, the form of the human head could be used to detect the location of maintenance personnel, and the robots' movements restricted such that no danger is presented to maintenance personnel. If more than one camera system is employed for detection, the precise spatial location of maintenance personnel can be detected. The robustness of the method which has been achieved under conditions of varying illumination shows that video sequence analysis has considerable potential for non-contact safeguarding of workers on highly automated installations.
wood working industry
Type of hazard:mechanical hazards
Catchwords:machine safety
Description, key words:non-contact protective device, finger detection, hand detection, video image-based detection, coarse-to-fine strategy, video image analysis