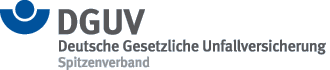
abgeschlossen 12/2012
An industrielle Produktionsanlagen werden zunehmend Anforderungen bezüglich größerer Wirtschaftlichkeit bei gleichzeitig flexiblen Produktionsabläufen gestellt. Veränderte Eigenschaften von Rohmaterialien, variable Produktspezifikationen oder veränderliche Interaktionen mit Bedienern werden dabei automatisch erfasst, um den weiteren Produktionsvorgang selbstständig anzupassen. Dieser Übergang von starren auf bedienerzentrierte, adaptive Automatisierungskonzepte führt zu neuen Herausforderungen in Bezug auf die Sicherheit und Verfügbarkeit der Anlage. In solchen intelligenten Produktionsumgebungen sind nicht mehr sämtliche Abläufe in der Steuerungssoftware enthalten, sondern der zeitliche Verlauf der genannten Randbedingungen zusammen mit den gewählten Adaptionsmechanismen bestimmt das jeweilige Maschinenverhalten. Dies erfordert spezielle Maßnahmen zur Aufrechterhaltung der Sicherheit. Die intensive Einbindung von Personal macht eine unmittelbare Interaktion von sich bewegenden Maschinenteilen und dem Menschen notwendig. Dies ist zum einen traditionell eine wichtige Maßnahme, um eine hohe Flexibilität der Anlage zu erreichen; zum anderen führt sie aber zu sehr hohen Anforderungen an die Sicherheit. Das Ziel des Verbundprojektes EsIMiP: Die Produktionsbewegungen der Maschine werden durch autonom agierende Komponenten des maschinellen Lernens sowie der Online-Berechnung adaptierender Algorithmen gesteuert. Die Steuersignale der zuvor genannten „unsicheren" Komponenten werden danach stets durch eine deterministische „sichere" Steuerung überprüft. Diese übernimmt bei gefahrbringender Annäherung an den Menschen die Kontrolle über die Maschinenbewegungen und stoppt gegebenenfalls.
In EsIMiP wurde eine innovative Steuerungsmethode entwickelt, um die sichere Zusammenarbeit von Mensch und bewegten Maschinen ohne trennende Schutzeinrichtungen zu ermöglichen. Dazu wurden realistische Modelle des menschlichen Bewegungsverhaltens im Arbeitsumfeld erstellt und für die Online-Berechnung der Steuerstrategien verwendet. Aufgrund des nicht deterministischen menschlichen Verhaltens war es notwendig, probabilistische Menschmodelle zu verwenden und die Algorithmen zu optimalen und sicheren Steuerstrategien auf diesen Modelltyp anzupassen. Für den Menschen sicherheitskritische Prozesszustände, in denen die Maschine stoppen müsste, werden frühzeitig antizipiert und z. B. durch Ausweichbewegungen verhindert. Bedingung dafür war, dass der Mensch in seiner realen industriellen Umgebung in Echtzeit, zuverlässig und ohne weitere Hilfsmittel (wie Marker oder Hintergrundmuster) erkannt und seine Positionen und Arbeitsstellungen ausreichend genau vermessen werden konnte. Es wurden daher mehrere Sensoren – auch mit unterschiedlichem Funktionsprinzip – eingesetzt, damit keine Verdeckungen durch Objekte im Arbeitsraum (z. B. auch andere Menschen) auftreten können. Das menschliche Bewegungsverhalten wurde in verschiedenen Kontexten (konstantes vs. variables Roboterverhalten) betrachtet. Mehrere Einflussfaktoren auf die Akzeptanz des Arbeitssystems wurden bestimmt und mithilfe von Probandenversuchen näher beleuchtet. Beim IFA wurden Probandenversuche mit virtuellen Roboterarbeitsplätzen durchgeführt. Als notwendige technische Plattform wurden am Roboter spezialisierte und hoch zuverlässige Industriesteuerungen eingesetzt und weiterentwickelt. Alle Entwicklungen wurden an einem Arbeitsplatz mit einem kollaborierendem Roboter implementiert und abschließend demonstriert.
Im Projekt wurde ein neuartiger Ansatz vorangetrieben, bei dem eine „Strategische Automatisierungskomponente" die Verfügbarkeit des Systems durch Erlernen von Steuerungsstrategien unter Einbezug des Verhaltens der Bedienpersonen und der Sicherheitsfunktionen erhöht. Gleichzeitig gewährleistet eine vom IFA mitentwickelte unabhängige „Operative Automatisierungskomponente" die Sicherheit des Gesamtsystems. Die Umgebung des Roboters wird dabei kontinuierlich überwacht. Dies ermöglicht eine Vorhersage über das Verhalten der Personen in der Produktionsumgebung und damit ein effizientes Produktionsverhalten des Roboters, das zugleich die Sicherheit des Gesamtsystems nicht beeinträchtigt. Die industriellen Projektpartner konnten wichtige Weiterentwicklungen im Umfeld der sicheren Antriebs-, Steuerungs- und Robotertechnik realisieren. Für die Überwachung des Arbeitsraums zeigte es sich als essenziell, dass die Art sowie die Platzierung der unterschiedlichen Sensoren zur Aufgabe passen, die das jeweilige System erfüllen soll. Die sichere Ultraschallsensorik wurde vom IFA direkt am Roboter platziert, um die sicherheitsrelevante Reduktion der Robotergeschwindigkeit zu bestimmen. Die unsichere Sensorik wurde durch extern platzierte Farbkameras für die Bewegungssteuerung realisiert. Diese ermitteln die durch Bedienpersonen belegten Bereiche der Arbeitszelle, um die Roboterbewegung kontinuierlich neu zu planen. Der Zusammenhang von Geschwindigkeit und Abstand kann dabei für jedes Objekt definiert werden. Die ergonomischen Untersuchungen des Projektes rückten zwei zentrale Aspekte in den Fokus: einerseits die Untersuchung des menschlichen Bewegungsverhaltens und andererseits die Analyse der Akzeptanz der Arbeitsform Mensch-Roboter-Kollaboration. Mithilfe der Untersuchungsergebnisse können systemergonomische Anforderungen spezifiziert und - durch die Implementierung der Erkenntnisse in die Steuerungsarchitektur und in die Gestaltung des Arbeitsplatzes - die Wahrscheinlichkeit von Fehlhandlungen des Menschen reduziert werden.
-branchenübergreifend-
Gefährdungsart(en):Mechanische Gefährdungen
Schlagworte:Unfallverhütung, Maschinensicherheit
Weitere Schlagworte zum Projekt:industrielle Produktionsanlagen, kollaborierende Roboter, adaptive Automatisierungskonzepte, sichere Ultraschallsensorik, Human Factors